Vicki Merlo: 35 Years with ISS School Supply
In July 2019, Vicki Merlo of our School Supply department will celebrate her 35th Anniversary with ISS. We recently asked Vicki to reflect on her career with ISS so far — her answers give a wonderful look into the adventures, changes, and colorful life of ISS School Supply over the years.
How did you get started in this career?
I graduated college in December 1983 and I was just looking for a steady job. My neighbors (Stella Taylor and Hilda Szmutko) both worked for ISS at the time and they needed some help in the Purchasing department and they knew I was looking for work. I was hired as a temp at first, to make sure I worked out….I guess I did, because they hired me full time and here we are 35 years later. I quickly realized I loved working here; I got to know what ISS was all about and I believed in its mission. I stayed because I loved the work and I felt that I was doing something worthwhile to help overseas schools. Plus, it was such a great work environment and great people.
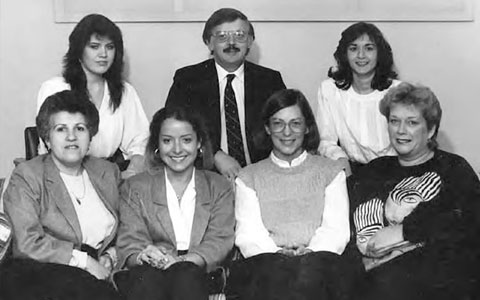
How did you typically process an order back then compared to what you do today?
VERY differently. There were no computers when I started, so everything was done manually by hand or on a typewriter. For purchase orders, we would receive hard copies sent a courier to us from the schools. We had a cover letter drafted for our suppliers (copies made using a mimeograph machine or carbon paper) on which we’d type certain information for each order, then we’d keep a copy of the cover letter and purchase order for ourselves while mailing the originals to the vendor. Eventually, the copier became the norm for making copies. We would spend hours and days preparing orders for mailing and creating folders for our files. Then when invoices arrived, we had to make around 8 copies, because we needed copies for our files, for accounting, and around 4-5 copies for shipping documents for our freight forwarder and the school. There were mounds of paper in our department. Everything now is in the computer and we are completely paperless. Orders get emailed and are acknowledged almost immediately. Back then it took about two weeks for us to receive an acknowledgment card in the mail (which we attached to our orders and requested to have returned).
I also remember when I started we had just gotten a fax machine and we were in awe that we could send a piece of paper through this machine and a copy would come out in another location. That’s how we communicated with our warehouse. The way things work now, the warehouse logs in freight directly into NAV and we see what’s arrived in real-time. Back when I first started, the warehouse would hand write on a sheet of paper all the receipts that they logged on that day. At the end of the day or the next morning, they would fax that sheet to us. Part of my job was to manually write up every receipt as individual “warehouse tickets” (we had special pads made for this purpose) so that we could attach each warehouse ticket to the appropriate order. Special hand-written notes were made in the files to keep track of order status.
When it was time to ship, we would go through every folder for every order and manually “pull” documents to add to our shipment. The warehouse tickets would all be put in a pile and then the pertinent receipt information from each warehouse ticket was typed on a shipment list. We’d then grab a partner and double-check that we typed the list correctly – one person would check the list while the other person read off the receipt information from the warehouse tickets. The totals from the vendor invoices would also have to be manually added using an adding machine (done twice to verify accuracy). For a large shipment, this whole process could sometimes take up to a week. With NAV, most of the work is already compiled in the computer ahead of shipping. Depending on the size of the shipment, preparation can take anywhere from a half-hour up to a day, unless there are special paperwork requirements, which may take a little longer.
Our operating systems have gone through several iterations since I started. When we finally became computerized, it was the AS/400 and we had one computer for the whole department at first. After the AS/400, we upgraded to an Oracle system, and finally, now, to NAV.
How many different people do you think you’ve served through the years? Are there any standout stories?
At one point, I know we were handling around 200 schools. I honestly can’t say how many total schools we’ve handled since I started. Some have left our service and then come back a few years later. Some schools have closed; there have been hundreds of schools that we’ve handled over the years.
As for standout stories, the one story that always stands out for me is the time we had to order a school van for a school in Taipei. It had to be driven into the container and it was a close fit. The only person who was thin enough to be able to get out was Art Flowers (who later became our warehouse manager for several years). As thin as he was, the only way he could get out of the van was to crawl out the window, climb off the top of the van and slide himself out of the container.
What was the oddest thing you ever ordered?
We’ve ordered lots of oddball items over the years, but the ones I remember are the ones with great stories behind them, like the van. There was another order I’ll never forget. One of our schools had ordered frogs, but we thought they were preserved frogs for dissection. Instead, we received LIVE frogs. Our warehouse manager (Don Kramer at the time) called us in a panic, screaming that there were frogs jumping all over the warehouse! Our warehouse was in Windsor, NJ at the time, so one of our staff members drove over to the warehouse, gathered up all the frogs, brought them back to our office and set them free in the creek next to our building. We saved some lives that day…
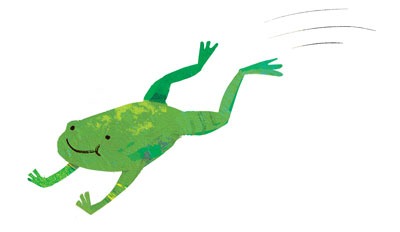
What is the most enjoyable aspect of your job?
I love the feeling when a shipment leaves; I always feel a sense of accomplishment when a school’s orders are on their way to their destination. Also, I really enjoy when I have to dig into something to research it. Whether it’s freight issues, a shipping process, figuring out a procedure, I really enjoy doing the “detective” work of trying to figure out a problem and coming up with a solution.
What advice would you give to someone who is ordering school supplies for the first time?
International shipping has its challenges, so don’t be afraid to ask questions; no question is a dumb question. They should also check on their receiving country’s import requirements because it’s better to know upfront if there are items that have restrictions or license requirements for import so there are no surprises when we go to ship. Also, plan ahead: A timeline for ordering needs to be established by working backward. When do you need the goods on-site? How long does customs clearance normally take? From there we can determine when the goods need to arrive at the port, transit time, the time allowed for consolidation of goods at ISS from the vendors, and finally, when the orders are needed to be emailed to ISS to begin processing.
Anything else you want to share?
One thing that has never changed in all the years I’ve been here is the dedication of the ISS staff. People here really do take pride in what they do and I think that’s why so many people have worked here for many years.
We’re grateful for all the stories you have to share, and look forward to those still to come.
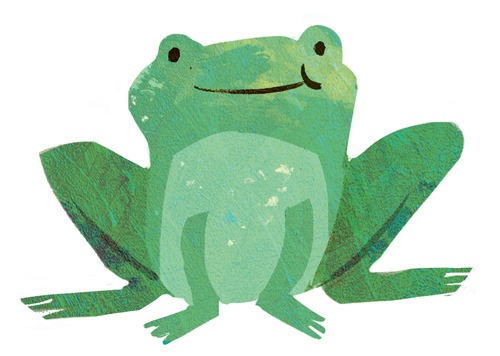
If you’d like to learn more about ISS School Supply or how they could help with your campus’ needs,
visit our school supply page or email SchoolSupply@ISS.edu.